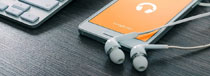
郵箱:2897013274@qq.com
地址:四川省成都市武侯區(qū)武侯大道順江段77號
鋼結構制作施工工藝
鋼結構制作施工工藝
1.0.6.1 工藝流程
1.0.6.2 制作工藝
(1)放樣、號料
1)熟悉施工圖,并認真閱讀技術要求及設計說明,并逐個核對圖紙之間的尺寸和方向
等。特別應注意各部件之間的連接點、連接方式和尺寸是否-一對應。發(fā)現(xiàn)有疑問之處,應
與有關技術部門聯(lián)系解決。
2)準備好做樣板、樣桿的材料,一般可采用薄鋼板和小扁鋼。
3)放樣需用的工具:尺、石筆、粉線、劃針、劃規(guī)、鐵皮剪等。尺必須經過計量部門
的校驗復核,合格后方可使用。
4)號料前必須了解原材料的材質及規(guī)格,檢查原材料的質量。不同規(guī)格、不同材質的
零件應分別號料。并依據先大后小的原則依次號料。
5)樣板、樣桿上應用油漆寫明加工號、構件編號、規(guī)格,同時標注上孔直徑、工作線、
彎曲線等各種加工符號。
6)放樣和號料應預留收縮量(包括現(xiàn)場焊接收縮量)及切割、銑端等需要的加工余量。
銑端余量:剪切后加工的一般每邊加3~4mm,氣割后加工的則每邊加4~5mm。
切割余量:自動氣割割縫寬度為3mm,手工氣割割縫寬度為4mm(與鋼板厚度有關)。
焊接收縮量根據構件的結構特點由工藝給出。
7)主要受力構件和需要彎曲的構件,在號料時應按工藝規(guī)定的方向取料,彎曲件的外
側不應有樣沖點和傷痕缺陷。
8)號料應有利于切割和保證零件質量。
9)本次號料后的剩余材料應進行余料標識,包括余料編號、規(guī)格、材質及爐批號等,
以便于余料的再次使用。
10)放樣和樣板、樣桿允許偏差如表1.0.6.2-1 所示:
11)號料后允許偏差如表1.0.6.2-2 所示:
(2)切割
1)下料劃線以后的鋼材,必須按其所需的形狀和尺寸進行下料切割。常用的切割方法
有:機械切割:使用剪切機、鋸割機、砂輪切割機等機械設備(主要用于型材及薄鋼板的切
割)。
氣割:利用氧氣一乙炔、丙烷、液化石油氣等熱源進行(主要用于中厚鋼板及較大斷面
型鋼的切割)。
等離子切割:利用等離子弧焰流實現(xiàn)(主要用于不銹鋼、鋁、銅等金屬的切割)。
2)剪切時應注意以下工藝要點:
A.剪刀口必須鋒利,剪刀材料應為碳素工具鋼和合金工具鋼,發(fā)現(xiàn)損壞或者遲鈍需及
時檢修、磨礪或調換。
B.上下刀刃的間隙必須根據板厚調節(jié)適當。
C.當一張鋼板上排列許多個零件并有幾條相交的剪切線時,應預先安排好合理的剪切
程序后再進行剪切。
D.剪切時,將剪切線對準下刃口,剪切的長度不能超過下刀刃長度。
E.材料剪切后的彎扭變形,必須進行矯正;剪切面粗糙或帶有毛刺,必須修磨光潔。
F.剪切過程中,切口附近的金屬,因受剪力而發(fā)生擠壓和彎曲,從而引起硬度提高,
材料變脆的冷作硬化現(xiàn)象,重要的結構件和焊縫的接口位置,一定要用銑、刨或砂輪磨削等
方法將硬化表面加工清除。
3)鋸切機械施工中應注意以下施工要點:
A.型鋼應經過校直后方可進行鋸切。
B.所選用的設備和鋸條規(guī)格,必須滿足構件所要求的加工精度。
C.單件鋸切的構件,先劃出號料線,然后對線鋸切,號料時,需留出鋸槽寬度(鋸槽
寬度為鋸條厚度加0.5~1.0mm)。成批加工的構件,可預先安裝定位擋板進行加工。
D.加工精度要求較高的重要構件,應考慮預留適當?shù)募庸び嗔?,以供鋸切后進行端面
精銑。
E.鋸切時,應注意切割斷面垂直度的控制。
4)氣割操作時應注意以下工藝要點:
A.氣割前必須檢查確認整個氣割系統(tǒng)的設備和工具全部運轉正常,并確保安全。在氣
割過程中應注意:
a.氣壓穩(wěn)定,不漏氣。
b.壓力表、速度計等正常無損。
C.機體行走平穩(wěn),使用軌道時要保持平直和無振動。
d.割嘴氣流暢通,無污損。
e.割炬的角度和位置準確。
B.氣割時應選擇正確的工藝參數(shù)(如割嘴型號、氣體壓力、氣割速度和預熱火焰能率
等),工藝參數(shù)的選擇主要是根據氣割機械的類型和可切割的鋼板厚度進行確定。
C.切割時應調節(jié)好氧氣射流(風線)的形狀,使其達到并保持輪廓清晰、風線長和射
力高。
D.氣割前,應去除鋼材表面的污垢、油污及浮銹和其他雜物,并在下面留出一定的空
間,以利于熔渣的吹出。氣割時,割炬的移動應保持勻速,割件表面距離焰心尖端以2~5mm
為宜。
E.氣割時,必須防止回火。
F.為了防止氣割變形,操作中應遵循下列程序:
a.大型工件的切割,應先從短邊開始。
b.在鋼板上切割不同尺寸的工件時,應靠邊靠角,合理布置,先割大件,后割小件。
c.在鋼板上切割不同形狀的工件時,應先割較復雜的,后割較簡單的.
d.窄長條形板的切割,采用兩長邊同時切割的方法,以防止產生旁彎(俗稱馬刀彎)。
5)機械切割和氣割的允許偏差見表1.0.6.2-3、表1.0.6.2-4。
(3)矯正和成型
1)碳素結構鋼在環(huán)境濕度低于-16℃、低合金結構鋼在環(huán)境濕度低于-12℃時,不應
進行冷矯正和冷彎曲。碳素結構鋼和低合金結構鋼在加熱矯正時,加熱濕度不應超過900℃。
低合金結構鋼在加熱矯正后應自然冷卻。
2)當零件采用熱加工成型時,加熱濕度控制在900~1000℃;碳素結構鋼和低合金結
構分別下降到700℃和800℃之前,應結束加工。
3)矯正后鋼材表面,不應有明顯的凹面損傷,劃痕深度不得大于0.5mm,且不應大于
該鋼材厚度負允許偏差的1/2。
4)冷矯正和冷彎曲的最小曲率半徑和最大曲矢高應符合表1.0.6.2-5 的要求。
5)鋼材矯正后的允許偏差,應符合表1.0.6.2-6 要求
(4)邊緣加工
1)氣割或機械剪切的零件,需要技能型邊緣加工時,其刨削量不應小于2.0mm
2)焊接坡口加工宜采用自動切割、半自動切割、坡口機、刨邊等方法進行。
3)邊緣加工一般采用銑、刨等方式加工。邊緣加工時應注意控制加工面的垂直和表面
粗糙度。
(5)管球加工
1)螺栓球成型后,不應有裂紋、褶皺、過燒。
2)鋼板壓成半圓球后,表面不應有裂紋、褶皺;焊接球其對接坡口應采用機械加工,
對接焊縫打磨平整。
3)鋼管坡口的切割及相貫線的切割,可采用相貫線自動切割機進行加工。
圖1.0.6.2-2 邊緣加工允許偏差
4)螺栓球加工的允許偏差應符合表1.0.6.2-8 的規(guī)定。
5)焊接球加工的允許偏差應符合表1.0.6.2-9 的規(guī)定
6)鋼網架(桁架)用鋼管桿件加工的允許偏差應符合表1.0.6.2-10 的規(guī)定。
1)采用鉆模制孔和劃線制孔兩種方法。較多頻率的孔組要設計鉆模,以保證制孔過程
中的質量要求。制孔前考慮焊接收縮余量及焊接變形的因素,將焊接變形均勻地分布在構件
上。
2)A、B 級螺栓孔(二類孔)應具有H12 的精度,孔壁表面粗糙度Ra 不應大于12.5μ
m。其孔徑的允許偏差應符合表1.0.6.2-11 的要求。
3)C級螺栓孔(Ⅱ類孔),孔壁表面粗糙度Ra不應大于25μm其允許偏差應符合表1.0.6.2
-12 的規(guī)定。
2.對接接頭在拼接板一側的螺栓孔為一組。
3.在兩相鄰節(jié)點或接頭間的螺栓孔為一組,但不包括上述兩款規(guī)定的螺栓孔。
4.受彎構件翼緣上的連接螺栓孔,每米長度范圍內的螺栓孔為一組。
5)螺栓孔孔距的允許偏差超過上表規(guī)定的允許偏差時,應采用與母材材質相匹配的焊
條補焊,并經超聲波探傷(UT)合格后,重新制孔。
(7)摩擦面加工
1)采用高強度螺栓連接時,應對構件摩擦面進行加工處理。處理后的抗滑移系數(shù)應符
合設計要求。
2)高強度螺栓連接摩擦面的加工,可采用噴砂、拋丸和砂輪機打磨等方法(注:砂輪
機打磨方向應與構件受力方向垂直,且打磨范圍不得小于螺栓直徑的4 倍)。
3)經處理的摩擦面應采取防油污和損傷保護措施。
4)制造廠和安裝單位應分別以鋼結構制造批進行抗滑移系數(shù)試驗。制造批可按分部(子
分部)工程劃分規(guī)定的工程量每2000t 為一批,不足2000t 的可視為一批。選用兩種及兩種
以上表面處理工藝時,每種處理工藝應單獨檢驗。每批三組試件。
5)抗滑移系數(shù)試驗用的試件應由制造廠加工,試件與所代表的鋼結構構件應為同一材
質、同批制作、采用同一摩擦面處理工藝和具有相同的表面狀態(tài),并應用同批同一性能等級
的高強度螺栓連接副,在同一環(huán)境條件下存放。
6)試件鋼板的厚度,應根據鋼結構工程中有代表性的板材厚度來確定。試件板面應平
整,無油污,孔和板的邊緣無飛邊、毛刺。
7)制作廠應在鋼結構制作的同時進行抗滑移系數(shù)試驗,并出具報告。試驗報告應寫明
試驗方法和結果。
8)應根據國家標準《鋼結構高強度螺栓連接的設計、施工及驗收規(guī)程》(JGJ82)的要
求或設計文件的規(guī)定,制作材質和處理方法相同的復驗抗滑移系數(shù)用的試件,并與構件同時
移交。
(8)端部加工
1)構件的端部加工應在矯正合格后進行。
2)應根據構件的形式采取必要的措施,保證銑平端面與軸線垂直。
3)端部銑平的允許偏差,應符合表1.0.6.2-14 的要求。
(9)鋼結構構件的組裝
1)鋼結構構件組裝的一般規(guī)定:
A.組裝前,工作人員必須熟悉構件施工圖及有關的技術要求,并根據施工圖要求復核
其需組裝零件質量。
B.由于原材料的尺寸不夠,或技術要求需拼接的零件,一般必須在組裝前拼接完成。
C.在采用胎模裝配時必須遵循下列規(guī)定:
a.選擇的場地必須平整,并具有足夠的剛度。
b.布置裝配胎模時必須根據其鋼結構構件特點考慮預放焊接收縮量及其他各種加工余
量。
C.組裝出首批構件后,必須由質量檢查部門進行全面檢查,經檢查合格后,方可進行
繼續(xù)組裝。
d.構件在組裝過程中必須嚴格按照工藝規(guī)定裝配,當有隱蔽焊縫時。必須先行施焊,
并經檢驗合格后方可覆蓋。當有復雜裝配部件不易施焊時,亦可采用邊裝配邊施焊的方法來
完成其裝配工作。
e.為了減少變形和裝配順序,可采取先組裝成部件,然后組裝成構件的方法。
2)鋼結構構件組裝方法的選擇,必須根據構件的結構特性和技術要求,結合制造廠的
加工能力、機械設備等情況,選擇能有效控制組裝質量、生產效率高的方法進行。
3)典型結構組裝
A,焊接H 形鋼施工工藝
a 工藝流程
b.工藝要求
a)下料
①下料前應將鋼板上的鐵銹、油污清除干凈,以保證切割質量。
②鋼板下料宜采用多頭切割機幾塊板同時下料,以防止零件產生馬刀彎。
③鋼板下料應根據配料單規(guī)定的規(guī)格尺寸落料,并適當考慮構件加工時的焊接收縮余
量。
④開坡口
采用坡口倒角機或半自動切割機,全熔透焊縫坡口角度如圖1.0.6.2.3(左)所示。熔透
焊縫坡口角度如圖1.0.6.2-3(右)所示。
圖1.0.6.2-3 焊接H 形鋼全熔透和半熔透焊接縫坡口角度
⑤ 下料后,將割縫處的流渣清除干凈,轉入下道工序。
b)裝配BH 梁裝配在組裝平臺上進行,平臺簡如圖1.0.6.2-4。
裝配前,應先將焊接區(qū)域內的氧化皮、鐵銹等雜物清除干凈;然后用石筆在翼緣板上劃
線,標明腹板裝配位置,將腹板、翼緣板置于平臺上,用楔子、角尺雕BH 梁截面尺寸及垂
直度,裝配間隙控制在2~4mm(半熔透焊縫、貼角焊不留間隙),點焊固定翼緣板,再用
角鋼點焊固定。點焊焊材材質應與主焊縫材質相同,長度50mm 左右,間距300mm,焊縫
高度不得大于6mm,且不超過設計高度的2/3。
C)焊接
①BH 梁焊接采用CO2 氣體保護焊打底,埋弧自動焊填充、蓋面,船形焊施焊的方法。
②工藝參數(shù)應參照工藝評定確定的數(shù)據,不得隨意更改。
③焊接順序:
○a打底焊一道;○b 填充焊一道;○c 碳弧氣刨清根;○d 反面打底、填充、蓋面;○e 正面填充、蓋面焊。
簡圖如圖1.0.6.2-5。
具體施焊時還要根據實際焊縫高度,確定填充焊的次數(shù),構件要勤翻身,防止構件產生
扭曲變形。如果構件長度>4m,則采用分段施焊的方法。
d)矯正
①BH 梁焊接后容易產生撓曲變形、翼緣板與腹板不垂直、薄板焊接還會產生波浪形等
焊接變形,因此一般采用機械矯正及火焰加熱矯正的方法矯正。
②機械矯正
矯正前,應清掃構件上的一切雜物,與壓輥接觸的焊縫焊點修磨平整。
使用機械矯正(翼緣矯正機)注意事項:構件的規(guī)格應在矯正機的矯正范圍之內,即:
翼緣板最大厚度≤50mm;翼緣板寬度=180~800mm;腹板厚度≤50mm;腹板高度>350mm
以上;工件材質:Q235(Q345 時被矯正板厚為Q235 的70%)
工件厚度與寬度須符合表1.0.6.2-15 的對應關系:
當翼緣板厚度超過30mm 時,一般要求往返幾次矯正(每次矯正量1~2mm)。
機械矯正時,還可以采用壓力機根據構件實際變形情況直接矯正。
③火焰矯正注意事項:○a 根據構件的變形情況,確定加熱的位置及加熱順序;○b 加熱
溫度最好控制在600~650℃。
e)二次下料
目的:確定構件基本尺寸及構件截面的垂直度,作為制孔、裝焊其他零件的基準。
當BH 梁截面小于750mm×520mm 時,可采用鋸切下料,當BH 截面大于750mm×
520mm 時,可采用銑端來確定構件長度。注意:二次下料時根據工藝要求加焊接收縮余量。
f)制孔:
①構件小批量制孔,先在構件上劃出孔的中心和直徑,在孔的圓周上(90°位置)打四
個沖眼,作鉆孔后檢查用,中心沖眼應大而深。
②當制孔量比較大時,要先制作鉆模,再鉆孔;制作鉆模的原則:
○a 同一類孔超過50 組;
○b 一組孔由8 個以上孔組成;
○c 重要螺栓孔。
③鉆孔時,擺放構件的平臺要平整,以保證孔的垂直度。
g)裝焊其他零件
h)最后校正構件,將構件表面的焊疤、焊瘤、飛濺等雜物清理干凈,即可出車間。
B.箱形截面構件的加工工藝
a. 放樣、下料
a)放樣
應按照圖紙尺寸及加工工藝要求增加加工余量(加工余量包含銑端余量和焊接收縮余
量)。以下發(fā)的鋼板配料表為依據,在板材上進行放樣、劃線。放樣前應將鋼材表面的塵土、
銹皮等污物清除干凈。
b)下料
對箱體的四塊主板(為了防止其馬刀變形)采用多頭自動切割機進行下料,對箱體上其
他零件的厚度在大于12mm 以上者采用半自動切割機開料,小于或等于12mm 以下者采用
剪床下料。氣割前應將鋼材切割區(qū)域表面的鐵銹、污物等清除干凈,氣割后應清除熔渣和飛
濺物。
b.開坡口
根據加工工藝卡的坡口形式采用半自動切割機或倒邊機進行開制。坡口一般分為全熔透
和非全熔透兩種形式。為了保證最終的焊接質量,對全熔透坡口的長度應在設計長度的基礎
上與非全熔透坡口相鄰處適當加長。
坡口切割后,所有的熔渣和氧化皮等雜物應清除干凈,并對坡口進行檢查。如果切割后
的溝痕超過了氣割的允許偏差,應用規(guī)定的焊條進行修補,并與坡口面打磨平齊。
c.矯正
對所下的板件用立式液壓機進行矯正,以保證其平整度。對鋼板有馬刀彎者應采用火焰
矯正的方法進行矯正,火焰矯正的溫度不得超過650℃。
d.銑端、制孔
工藝隔板的制作:箱體在組裝前應對工藝隔板進行銑端,目的是保證箱形的方正和定位
以及防止焊接變形。
e.箱體組裝
組裝前應將焊接區(qū)域范圍內的氧化皮、油污等雜物清理干凈。箱體組裝時,點焊工必須
嚴格按照焊接工藝規(guī)程執(zhí)行,不得隨意在焊接區(qū)域以外的母材上引弧。
a)將箱體組裝為槽形
先在裝配平臺上將工藝隔板和加勁板裝配在一箱體主板上,工藝隔板一般距離主板兩端
頭200mm,工藝隔板之間的距離為1000~1500mm,如圖1.0.6.2-6。此時所選主板根據箱
形截面大小不同而有選擇性:當截面≥800mm×800mm 時,選擇任意一塊主板均可;當截
面<800mm×800mm 時,則只能選擇與加勁板不焊一邊相對的主板。
組裝槽形:在組裝槽形前應將工藝隔板、加勁板與主板進行焊接。將另兩相對的主板組
裝為槽形,如圖1.0.6.2-7。
槽形內的工藝隔板、加勁板與主板的焊接:根據焊接工藝的要求用手工電弧焊或二氧化
碳氣體保護焊進行焊接。
b)組裝箱體的蓋板
在組裝蓋板前應對加勁板的三條焊縫進行無損檢驗,同時也應檢查槽形是否扭曲,直至
合格后方可組裝蓋板。
c)箱體四條主焊縫的焊接
四條主焊縫的焊接應嚴格按照焊接工藝的要求施焊,焊接采用二氧化碳氣體保護焊進行
打底,埋弧自動焊填充蓋面。在焊縫的兩端應設置引弧和引出板,其材質和坡口形式應和焊
件相同。埋弧焊的引弧和引出焊縫應大于50mm。焊接完畢后應用氣割切除引弧和引出板,
并打磨平整,不得用錘擊落。
對于板厚大于50mm 的碳素鋼和板厚大于36mm 的低合金鋼,焊接前應進行預熱,焊
后應進行后熱。預熱溫度宜控制在100~150℃預熱區(qū)在焊道兩側,每側寬度均應大于焊件
厚度的2 倍,且不應小于100mm。高層鋼結構的箱形柱與橫梁連接部位,因應力傳遞的要
求,設計上在柱內設加勁板,箱形柱為全封閉形,在組裝焊接過程中,每塊加勁板四周只有
三邊能用手工焊或CO2 氣體保護焊與柱面板焊接,在最后一塊柱面板封焊后,加勁板周邊
缺一條焊縫,為此必須用熔嘴電渣焊補上。為了達到對稱焊接控制變形的目的,一般留兩條
焊縫用電渣焊對稱施焊。
f.矯正、開箱體端頭坡口
箱體組焊完畢后,如有扭曲或馬刀彎變形,應進行火焰矯正或機械矯正。箱體扭曲的機
械矯正方法為:將箱體的一端固定而另一端施加反扭矩的方法進行矯正,如圖1.0.6.2-8。
對箱體端頭要求開坡口者在矯正之后才進行坡口的開制。
圖1.0.6.3-8 箱體組裝
g.箱體其他零件的組裝焊接。
h.構件的清理、掛牌以及構件的最終尺寸驗收、出車間。
C.勁性十字柱的加工工藝
十字柱加工流程圖如下。
a.下料:按照圖紙尺寸及加工工藝要求增加的加工余量,采用多頭切割機進行下料,
以防止零件產生馬刀彎。對于部分小塊零件板則采用半自動切割機或手工切割下料。
b.開坡口:根據腹板厚度的不同,采用不同的坡口形式。具體坡口形式由技術部門編
制相應的加工工藝卡。坡口采用半自動切割機進行開制。切割后,所有的流掛、飛濺、棱邊
等雜物均要清除干凈,方可進行下道工序。
c. H 形鋼和T 形鋼部件的制作
①H 形鋼的制作
○a 組裝:坡口開制完成,零件檢查合格后,在專用胎具上組裝H 形鋼。組裝時,利用
直角尺將翼緣的中心線和腹板的中心線重合,點焊固定。組裝完成后,在H 形鋼內加一些
臨時固定板,以控制腹板和翼緣的相對位置及垂直度,并起到一定的防變形作用。見圖1.0.6.2
-9。
○b 焊接:H 形鋼的焊接采用你氣體保護焊打底,埋弧自動焊填充、蓋面的方式進行焊
接。在焊接過程中要隨時觀察H 形鋼的變形情況,及時對焊接次序和參數(shù)進行調整。
○c 矯正:H 形鋼焊接完成后,采用翼緣矯正機對H 形鋼進行矯直及翼緣矯平,保證翼
緣和腹板的垂直度。對于扭曲變形,則采用火焰加熱和機械加壓同時進行的方式進行矯正。
火焰矯正時,其溫度不得超過650℃。
②T 形鋼的制作
T 形鋼的加工,根據板厚和截面的不同,可采用不同的方法進行。一般情況下采用先組
焊H 型鋼,然后從中間割開,形成2 個T 形鋼的方法加工。切割時,在中間和兩端各預留
50mm 不割斷,待部件冷卻后再切割。切割后的T 形鋼進行矯直、矯平及坡口的開制。如圖
1.0.6.2-10:
③H 形鋼、T 形鋼銑端:矯正完成后,對H 形鋼和T 形鋼進行銑端。
d.勁性十字柱的組裝
①工藝隔板的制作;在十字柱組裝前,要先制作好工藝隔板,以方便十字柱的裝配和定
位。工藝隔板與構件的接觸面要求銑端,邊與邊之間必須保證成90o 直角,以保證十字柱截
面的垂直度,見圖1.0.6.2-11。
②首先檢查需裝配用的H 形鋼是否矯正合格,其外形尺寸是否達到要求經檢查合格,
并將焊接區(qū)域內的所有鐵銹、氧化皮、飛濺、毛邊等雜物清除干凈后,方可開始組裝十字柱。
隔板的制作。
③將H 形鋼放到裝配平臺上,把工藝隔板裝配到相應的位置。將T 形鋼放到H 形鋼上,
利用工藝隔板進行初步定位,見圖1.0.6.2-12。
對于無工藝隔板而有翼緣加勁板的十字柱,先采用臨時工藝隔板進行初步定位,然后用
直角尺和卷尺檢查外形尺寸合格后,將加勁板裝配好,待十字柱焊接完成后,將臨時工藝隔
板去除,見圖1.0.6.2-13。
○4 利用直角尺和卷尺檢查十字柱端面的對角線尺寸和垂直度以及端面的平整度。對不
滿足要求的進行調整。
⑤經檢查合格后,點焊固定。
e. 勁性十字柱的焊接:采用CO2 地氣體保護焊進行焊接。焊接前盡量將十字柱底面墊
平。焊接時要求從中間向兩邊雙面對稱同時施焊,以避免因焊接造成彎曲或扭曲變形。
f. 十字柱的矯正:焊接完成后檢查十字柱是否產生變形如發(fā)生變形,則用壓力機進行機
械矯正或米用火焰矯正,火焰矯正時,加熱溫度控制在650℃。扭曲變形矯正時,一端固定,
另一端采用液壓千斤頂進行矯正,見圖1.0.6.2-14。
g.十字柱的銑端:矯正完成后,對十字柱的上端進行銑端,以控制柱身長度。
h.十字柱銑端完成后,將臨時工藝隔板去除,并將點焊縫打磨平整。
i.清理:十字柱裝配、焊接、矯正完成后,將構件上的飛濺、焊疤、焊瘤及其他雜物
清理干凈。
D.圓管加工工藝
a.卷管前應根據工藝要求對零件和部件進行檢查,合格后方可進行卷管。卷管前將鋼
板上的毛刺、污垢、松動鐵銹等雜物清除干凈后方可卷管。
b.對于>30mm 的鋼板在零件下料時根據具體情況,在零件的相關方向增加引板。其
引板的長度一般為50~100mm。
c.卷管加工
①一般卷管工藝流程圖
②卷管加工工藝流程說明
下料:
○a 以管中徑計算周長,下料時加2mm 的橫縫焊接收縮余量。長度方向按每道環(huán)縫加
2mm 的焊接收縮余量。
○b 采用半自動切割機切割,嚴禁手工切割。
○c 切割的尺寸精度要求如表1.0.6.2 - 16 。
○a 一般情況下,16mm 以下的鋼板均采用單坡口的形式,外坡口和內坡口兩種形式均
可。出于焊接方面的考慮,一般開外坡口,內部清根后焊接。
○b 大于16mm 的鋼板(不含16mm 的鋼板)可開雙坡口,也可根據設計要求開坡口。
○c 均采用半自動切割機切割坡口,嚴禁手工切割坡口。坡口切割完畢后要檢查板材的
對角線誤差值是否在規(guī)定的允許范圍內。如偏差過大,則要求進行修補。
○d 坡口的允許偏差要求如表1.0.6.2-17。
○e 坡口的加工方法可以采用磁力切割機沿管壁切割、采用半自動切割機在鋼板上切
割、采用坡口機切割鋼板坡口。
卷管:
○a 用CDW11HNC-50×2500 型卷板機進行預彎和卷板。
○b 根據實際情況進行多次往復卷制,采用靠模反復進行檢驗,以達到卷管的精度。
○c 卷制成型后,進行點焊,點焊區(qū)域必須清除掉氧化鐵等雜質,點焊高度不準超過坡
口的2/3 深度。點焊長度應為80~100mm。點焊的材料必須與正式焊接時用的焊接材料相
一致。
○d 卷板接口處的錯邊量必須小于板厚的10%,且不大于2mm。如大于2mm,則要求
進行再次卷制處理。在卷制的過程中要嚴格控制錯邊量,以防止最后成型時出現(xiàn)錯邊量超差
的現(xiàn)象。
○e 上述過程結束后,方可從卷板機上卸下卷制成形的鋼管。
焊接:
○a 焊接材料必須按說明書中的要求進行烘干,焊條必須放置在焊條保溫桶內,隨用隨
取。
○b 焊接時,焊工應遵守焊接工藝規(guī)程,不得自由施焊,不得在焊道外的母材上引弧。
○c 焊接時,不得使用藥皮脫落或焊芯生銹的焊條和受潮結塊的焊劑及已熔燒過的渣殼。
○d 焊絲在使用前應清除油污、鐵銹。
○e 焊條和焊劑,使用前應按產品說明書規(guī)定的烘焙時間和溫度進行烘焙。保護氣體的
純度應符合焊接工藝評定的要求。低氫型焊條經烘焙后應放入保溫筒內,隨用隨取。
○f 焊前必須按施工圖和工藝文件檢查坡口尺寸、根部間隙,焊接前必須清除焊接區(qū)的有
害物。
○g埋弧焊及用低氫焊條焊接的構件,焊接區(qū)及兩側必須清除鐵銹、氧化皮等影響焊接質
量的臟物。清除定位焊的熔渣和飛濺;熔透焊縫背面必須清除影響焊透的焊瘤、熔渣,焊根。
○h焊縫出現(xiàn)裂紋時,焊工不得擅自處理,應查出原因,制定出修補工藝后方可處理。
○i 焊縫同一部位的返修次數(shù),不宜超過兩次;當超過兩次時,應按專門制定的返修工藝
進行返修。
探傷檢驗:
○a 單節(jié)鋼管卷制、焊接完成后要進行探傷檢驗。焊縫質量等級及缺陷分級應符合設計
指導書中規(guī)定的《鋼結構工程施工質量驗收規(guī)范》的規(guī)定執(zhí)行。
○b 要求局部探傷的焊縫,有不允許的缺陷時,應在該缺陷兩端的延伸部位增加探傷長
度,增加的長度不應小于該焊縫長度的10%,且不應小于200mm;當仍有不允許的缺陷時,
應對該焊縫100%探傷檢查。
矯圓:
○a 由于焊接過程中可能會造成局部失圓,故焊接完畢后要進行圓度檢驗,不合格者要
講行矯圓。
○b 將需矯圓者放入卷板機內重新矯圓器,或采用矯圓器進行矯圓。矯圓器可以根據實
際管徑自制,采用絲桿頂彎。
組裝和焊接環(huán)縫:
○a 根據構件要求的長度進行組裝,先將兩節(jié)組裝一大節(jié),焊接環(huán)縫。
○b 環(huán)縫采用焊接中心來進行,卷好的鋼管必須放置在焊接滾輪架上進行,滾輪架采用
無級變速,以適應不同的板厚、坡口、管徑所需的焊接速度。
○c 組裝必須保證接口的錯邊量。一般情況下,組裝安排在滾輪架上進行,以調節(jié)接口
的錯邊量。
○d 接口的間隙控制在2~3mm,然后點焊。
○e 環(huán)縫焊接時一般先焊接內坡口,在外部清根。采用自動焊接時,在外部用一段曲率
等同外徑的槽鋼來容納焊劑,以便形成焊劑墊。
○f 根據不同的板厚、運轉速度來選擇焊接參數(shù)。單面焊雙面成型最關鍵是在打底焊接
上。焊后從外部檢驗,如有個別成型不好或根部熔合不好,可采用碳弧氣刨刨削,然后磨掉
碳弧氣刨形成的滲碳層,反面蓋面焊接或埋弧焊(雙坡口要進行外部埋弧焊)。
○g 焊接完畢后進行探傷檢驗,要求同前。
清理、編號:
○a 清理掉一切飛濺、雜物等。對臨時性的工裝點焊接疤痕等要徹底清除。
○b 在端部進行噴號,構件編號要清晰、位置要明確,以便進行成品管理。
○c 構件上要用紅色油漆標注X-X 和Y-Y 兩個方向的中心線標記。
鋼構件組裝允許偏差應符合國家標準《鋼結構工程施工質量驗收規(guī)范》(GB 50205-
2001)的要求。
(10)鋼結構預拼裝
1)鋼構件預拼裝工程可按鋼結構制作工程檢驗批的劃分原則劃分為一個或若干個檢驗
批。
2)預拼裝所用的支承凳或平臺應測量找平,檢查時應拆除全部臨時固定和拉緊裝置。
3)進行預拼裝的鋼構件,其質量應符合設計要求和相關國家標準的規(guī)定。
4)鋼結構制作單位應根據工程的結構特點及預拼裝單元的結構特性,編制詳細的預拼
裝方案。
5)預拼裝完成,經質量檢驗工程師、安裝代表及甲方、監(jiān)理檢驗合格后,方可拆除。